Mini Master
Mini Master is available in three models, capable of purifying 60 to 200 l/min of neat oil and 100 to 400 l/min of water-based emulsion, polluted by metal and non-metal particles. Excellent filtration capacity thanks to the disposable filter medium that can be modified as required. Characterised by a very small footprint, it is suitable for many industrial processes such as drawing, grinding, rolling, washing, polishing, etc.
LOSMA guarantees that each purifier is individually tested through rigorous control procedures. A quality and functional test certificate is issued for each unit.
All Master series models are equipped with a corrugated metal chain which, thanks to the side sealing discs, guarantees a perfect seal of the dirty liquid in the filter section.
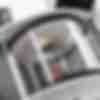
The filters in this series use a disposable filter medium, which allows the degree of filtration to be varied by changing only the type of filter, always achieving excellent results.
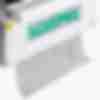
Compared to flatbed filters with the same flow rate, the Master range has a considerably smaller footprint and achieves a better degrees of filtration.
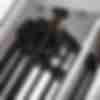
- In the initial phase the fabric, stretched inside the filter, is completely clean. The dirty liquid entering must pass through it into the lower tank, where it deposits the pollutants on its surface. The clean liquid then passes into the lower part where it finds the drain opening and falls into the collection tank. During this phase, the system is stationary and the belt does not advance. The pollutant material that settles there forms the actual filter layer, which in many applications can be up to 10 mm thick.
- In the intermediate phase, the filter fabric becomes dirty and its permeability is reduced because the dirty liquid continues to deposit pollutants on its surface. And so the liquid level starts to rise. The degree of filtration improves due to the thickness of sludge deposited. The system is also stationary in this phase.
- In the final phase, the liquid level has reached its maximum and the best possible degree of filtration has been achieved. The longer the filter runs in this condition, the better the average filtration will be. The system is also stationary in this phase. When the fabric is completely clogged and the liquid can no longer pass through, the regeneration cycle is started. The gear motor starts the system rotation and the dirty filter fabric is shifted with insertion of the clean one, the permeability is restored, the level drops and the system returns to the intermediate phase, starting the cycle again.
LOSMA guarantees that each purifier is individually tested through rigorous control procedures.
A quality and functional test certificate is issued for each unit.
Magnetic rotating disc pre-filtration system for separating magnetic pollutant particles from coolant.
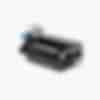
Eliminator of superficial oils allowing the quality of coolants to be maintained for a long time and eliminates odours generated in the presence of anaerobic bacterial flora.
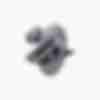
For supplying all utilities, controlling and managing all signals.
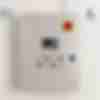
For clean liquid delivery from 0.1 bar to 100 bar.
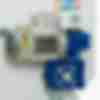
To collect the clean liquid to be returned to the machine tool.
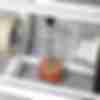
To collect dirty liquid for filter supply.
